L'innovation au service du souffleur en bouteilles dans le nord de la France au XIXe et au début du XXe siècle
Stéphane Palaude
Docteur en Histoire (France)
Gérard Caudrelier
Ex-consultant en économie sectorielle (France)
Le souffleur en bouteilles du nord de la France (Aisne, Marne, Nord) a bénéficié au cours du XIXe siècle et au début du XXe siècle d'une amélioration continuelle de ses conditions de travail sur le four par la mise au point d'une longue série d'innovations techniques, lesquelles lui ont permis, au final, de produire plus vite, mieux et davantage.
Innovations for the bottle glassblower in the North of France during the 19th and early 20th centuries
The bottle glassblower form the North of France (Aisne, Marne, Nord regions) benefits during the 19th and early 20th centuries from the continuous rise of standards in his working condition around the furnace, thanks to a long line of glassmaking innovation, permitting in turn better and faster production.
L'objet « bouteille » en verre creux n'a jamais vraiment été pris pour centre d'intérêt d'une étude scientifique quant à sa fabrication. Or, dans le nord de la France (Aisne, Marne et Nord) par exemple, celle-ci suit une évolution technique à part entière ayant pour but de permettre au verrier de produire mieux au XIXe et au début du XXe siècle, c'est-à-dire avant la mécanisation générale de la production, point que nous n'aborderons pas1. Nous avons préféré concentrer nos recherches sur les progrès antérieurs, à l'époque du travail du verre par l'homme, et non par une machine, qu'elle soit semi-automatique, comme la machine Boucher, ou automatique, telle la O'Neill ou la Lynch, sur laquelle l'homme n'est plus qu'un exécutant.
Pour cerner l'évolution au cours de laquelle sont adoptées successivement plusieurs innovations techniques permettant au souffleur d'améliorer sa cadence de fabrication et la qualité de son travail, nous reprendrons pour base de départ l'Encyclopédie de Diderot et d'Alembert, précisément le Recueil de planches, sur les sciences, les arts libéraux, et les arts méchaniques avec leur explication de 17722. Il n'est pas question de détailler la fabrication d'une bouteille à la verrerie de Sèvres au Bas-Meudon (Hauts-de-Seine), car les Encyclopédistes l'ont fait, mais de revenir sur les étapes : premier « cueillage », perçage, nouveaux prélèvements successifs pour accroître la masse de verre, marbrages répétés, soufflage en moule de fond, enfoncement de la piqûre, prise au pontil, réchauffage, pose de la cordeline, modelage de cette dernière, détachage et enfin transport de la pièce achevée jusqu'à l'arche à recuire. À partir de cette énumération, il devient possible de constater les améliorations.
En ce qui concerne le cueillage du verre, l'outil utilisé par le verrier n'a pas subi de modification puisqu'il est encore employé de nos jours sous sa forme première. Il s'agit d'un long tube métallique – la canne – dont l'officiant plonge l'extrémité renflée dans le bain de verre en fusion. Toutefois, si cet outillage n'a pas évolué, une importante transformation de l'appareil de fusion va affecter l'action de « cueiller » : la mise en service du four à bassin à fonte continue inventé par les Siemens. Le premier exemplaire connu se trouve à la verrerie en bouteilles de Vauxrot (Aisne) où, dès 1876, un four à pots à gaz « avec gazogène et récupérateur, système Ponsard » est expérimenté, puis transformé en four à bassin vers 18783. C'est cette même année que les Charbonneaux mettent en service leur four à bassin, dont nous ignorons le type exact, dans leur établissement en bouteilles de Cormontreuil, près de Reims (Marne). Dans le Nord, le premier four de type Siemens, mais avec « accumulateur de chaleur, [appelé] récupérateur à air chaud, système A. Charneau », est installé en 1884 à la verrerie Houtart, de Denain4. Alors qu'auparavant le niveau du verre baissait dans le creuset de fusion à mesure que le travail du verre s'effectuait, avec ce nouveau type de four, l'homme cueille désormais son verre toujours « à pot plein », puisque le bain de verre ne subit aucune variation de niveau dans ce gigantesque creuset à chargement et fonte perpétuels qu'est le bassin continu5. Il n'est plus besoin, en fin de journée, de se brûler les bras en allant cueiller au fond du pot.
Cet avantage a toutefois son revers. La réverbération et l'attaque continuelle des infrarouges sur les yeux des cueilleurs provoquent à la longue la « cataracte des verriers », comme le souligne Emilio Damour6. Afin d'en protéger les cueilleurs ainsi que de l'extrême chaleur, certains fours à bassin sont équipés dès la fin du XIXe siècle de « plongeurs » dans lesquels le verre est cueillé. Ces tubes en terre réfractaire qui s'enfoncent dans le bain de verre en fusion « sont emboîtés et lutés dans les ouvreaux qu'ils ferment hermétiquement »7. Il faut en attribuer l'invention à Claude Boucher, de Cognac, celui-là même qui créa la première machine semi-automatique opérationnelle8. Outre à Cognac où il est toujours attesté au tout début du XXe siècle par Jules Henrivaux, ce système des tubes plongeurs existe à la verrerie d'Albi (Tarn) en 19269. Nous n'en avons pas rencontré dans l'Aisne, la Marne ou le Nord, mais une étude approfondie de l'iconographie représentant l'intérieur des halles aux fours serait certainement instructive.
Cueillage, perçage, marbrage, l'homme prépare son verre avec la plus grande dextérité. Bien avant que n'apparaisse le four à bassin à fonte continue, la première innovation technique favorable au verrier consiste à laisser ce dernier placer sa paraison dans un moule de fond pour former presque définitivement l'objet par insufflation d'air pulmonaire dans la canne. L'utilisation de ce genre de moule remonte à l'époque romaine selon les traces archéologiques qui ont été mises à jour à travers l'Europe. Dans le cas de la fabrication des bouteilles à une période plus récente, le moule de fond est en métal ou en terre réfractaire. Son emploi permet de calibrer le fût du contenant. Il est présenté enterré dans le Recueil de planches de 1772. Ceci s'explique par le fait que le verrier œuvre au niveau du sol et qu'aux contacts répétés du verre chaud malléable, la terre réfractaire subit une dilatation et un retrait réguliers. Étant enserré dans sa gangue de terre, le moule de fond ne se fissure ni ne se rompt trop vite. Or, ce dernier est bientôt employé différemment.
À partir de 1790, le verrier de Quiquengrogne (Aisne) ne travaille plus le verre à même le sol de la halle au four, comme à Sèvres au Bas-Meudon dix-huit ans plus tôt. Il évolue désormais sur un plancher de travail, en bois ou en maçonnerie, lequel surplombe une fosse aux moules de fond dont le nombre s'est accru en fonction de la multiplication des modèles de bouteilles. S'ils sont en terre réfractaire, ces moules sont désormais cerclés de métal pour pallier toute rupture. S'ils sont en métal, la fonte est préférée, mais nous rencontrons aussi des moules en cuivre dont la conductibilité et la rapidité de refroidissement n'ont pas manqué d'être remarquées à Quiquengrogne chez Colnet, ou encore à Trélon (Nord) chez Mérode-Barbier de la Serre. Ces moules monoblocs doivent présenter un petit angle de dépouille pour faciliter la sortie de la pièce soufflée. Cela a pour effet de donner une forme légèrement tronconique au fût du futur contenant, ce qui nécessite un ultime marbrage pour gommer ce défaut. Les ouvriers verriers de Quiquengrogne utilisent toujours des moules de fond dans les années 1840.
Le 14 avril 1853, la veuve Leroy-Soyer, propriétaire de la verrerie en bouteilles de Masnières (Nord), prend un brevet pour des « moules à fonds de bouteilles » (n° 16103, fig. 1). Si le dessin qui accompagne le dépôt du brevet est très explicite, il semble que l'établissement de Masnières reprenne à son compte ce qui existe déjà, à moins que la diffusion de ce brevet n'ait été à ce point fulgurante pour que nous retrouvions un exemplaire en fonte de moule à fond de bouteille dans les collections du Musée d'histoire naturelle de Lille (inv. n° MI 7468/308, fig. 2a et 2b), donné vers 1856 par Vancauwelaert et Wagret, maîtres de verreries à Escautpont (Nord)10. Quant aux contenants présentant une piqûre (enfoncement plus ou moins prononcé du verre dans le fond), ce genre de moule en fonte présente l'avantage, lors du soufflage, de permettre, grâce au trou pratiqué au centre de sa base, l'évacuation de la vapeur d'eau et des fumées résultant de la combustion du matériau employé au fartage (voir plus loin), le centrage de la paraison et l'apparition d'un mamelon dont l'existence n'est pas anodine.
La présence d'un mamelon au fond de la piqûre d'une bouteille n'est pas vraiment récente. En 1840, la veuve Clicquot-Ponsardin réclame du maître de la verrerie d'Epinac (Saône-et-Loire) toute l'attention pour que cette « bulle » ne soit pas trop saillante. Pour réaliser celle-ci, le verrier dispose d'un outil particulier : la « molette ». Cette dénomination est demeurée à travers le temps, alors que l'objet n'a plus de commune apparence avec celui décrit en 1772. Il ne s'agit plus d'une petite tige métallique, mais désormais d'une espèce de clef à pipe à tête creuse, ainsi qu'elle est dessinée sur le brevet de la veuve Leroy-Soyer de 1853 et qu'elle est entrée dans les collections du Musée d'histoire naturelle de Lille vers 1856 (inv. n° MI 7436/276, fig. 3a, b et c). L'existence du mamelon pourrait d'ailleurs remonter plus loin encore. En effet, le peintre Develly a représenté une molette en forme de clef à pipe entre les mains d'un verrier de Sèvres au Bas-Meudon en 1820. Nous pensons toutefois que la tête de l'outil était alors pleine, et non creuse11.
Fig. 3 a, b, c. Molette de 1856 en situation ; © O. Boilly, Musée d'histoire naturelle de Lille, inv. n° MI 7436/276.
La standardisation des bouteilles est poussée très loin outre-Manche où l'Anglais Ricketts, de Bristol, dépose en 1821 le premier brevet de moule de soufflage complet, c'est-à-dire fût d'une bouteille et son épaulement compris. En France, la première mention de soufflage en moule complet remonte aux années 1820-1830, à la cristallerie de Baccarat (Meurthe-et-Moselle). En bouteillerie, il faut attendre 1840 pour apprendre que les frères Coutures utilisent des moules complets dans leur verrerie de Bordeaux (Gironde). Quant au premier exemplaire en fonte parvenu jusqu'à notre époque, il s'agit du moule Carillon de 1855, en trois parties (un moule de fond fixe et deux coquilles supérieures mobiles reliées par une charnière), déposé au Musée des arts et métiers (inv. n° 6438). Or, l'antériorité de ce moule est remise en question, car, dans le Nord, le maître de verreries d'Anzin, César Segard, dépose un brevet le 31 août 1854 pour « des moules à chariots, pour la fabrication des bouteilles » (n° 20641). Ces moules sont, soit en deux coquilles, soit en trois parties comme le moule Carillon. Segard a imaginé un dispositif de fermeture mécanique par mise en mouvement des coquilles mobiles fixées chacune sur un chariot. Il n'existe plus de charnières.
Dans ce genre de moule, le souffleur, tout en insufflant l'air de ses poumons dans la canne, doit tourner sa paraison continuellement pour gommer le défaut des coutures (jointures de coquilles). Un inventeur bordelais, Adolphe Cahuc, imagine alors de faire tourner le moule autour de la paraison. Il crée le premier « moule tournant » dont il prend deux brevets, le premier, le 19 septembre 1873 pour « un système de moule tournant pour la fabrication des bouteilles en verre » (n° 100436, avec certificat d'addition du 26 janvier 1877), et le second, le 18 septembre 1874 pour « un moule tournant à fond creux et pédale pour la fabrication des bouteilles en verre » (n° 100794). Tandis que le verrier maintient sa paraison en place dans le moule refermé au moyen d'un dispositif actionné par une pédale, un gamin tourne une manivelle dont le mouvement entraîne la rotation mécanique du corps du moule de soufflage complet. Dans les premiers mois de l'année 1878, Alain Chartier, de la verrerie de Dorignies, près de Douai (Nord), fait monter quelques places avec licence de Cahuc, à raison de 50 francs par mois et par moule12. Ce système semble lui convenir si bien qu'il obtient cession des deux brevets par Cahuc le 11 juin 187913. Selon Jules Henrivaux, Alain Chartier utilise les moules tournants Cahuc à Dorignies de 1878 à 189014. Ce système serait-il tombé en désuétude par la suite ? Nous ne le croyons pas car dès 1891 au moins, un moule tournant est employé dans la fabrication des bouteilles champenoises à la verrerie de Trélon. Rien n'indique qu'il s'agisse directement du moule tournant Cahuc, mais il y a de fortes chances que ce soit le cas. Nous n'envisageons pas que Louis Clavon, maître de verreries trélonais, ait adopté le moule tournant Boucher (brevet du 10 janvier 1881, n° 140513) pour lequel Jules Henrivaux ne mentionne d'utilisation qu'à la verrerie de Cognac, propriété de l'inventeur, de 1880 à 189315.
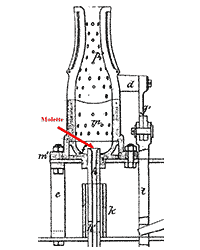
Fig. 4. Moule de soufflage complet et sa molette, brevet Petitjean du 10 décembre 1884, n° 165855, « Moule perfectionné pour la fabrication des bouteilles à Champagne ; © Institut national de la propriété industrielle. Cliché S. Palaude.
D'autres moules de soufflage complet vont apparaître, non tournants ceux-là. Il en est qui permettent même de façonner la bouteille la plus difficile à réaliser : la champenoise. Parmi ceux-ci, nous retiendrons le moule système Tronchet en service aux verreries de Vauxrot, Hirson (Aisne) et Fourmies (Nord) dès le début des années 1880 et pour longtemps (brevets n° 123773 du 10 avril 1878 et n° 132672 du 10 septembre 1879). Autre inventeur, Théodore Petitjean prend un brevet le 10 décembre 1884 pour « moule perfectionné pour la fabrication des bouteilles à Champagne » (n° 165855, fig. 4)16. Détail commun, depuis la mise au point du système Cahuc, tous les moules complets comportent des coquilles à raccords en lignes ondulées, ce qui facilite le gommage des coutures lorsque la paraison est tournée par le verrier dans le moule ou lorsque le moule tourne autour de celle-ci.
Afin de réduire les effets gênants inhérents au contact et au frottement de la paraison sur la paroi interne du moule métallique de formage complet, les verriers ont pris l'habitude de le « farter » pour assurer une meilleure « glisse ». Il s'agit d'y insérer un brin de paille ou quelques copeaux de bois avant d'y placer la paraison. Le matériau s'enflamme au premier contact du verre chaud, dégageant ainsi du carbone qui facilite le mouvement de rotation de la paraison dans le moule17. Mais Xavier de Heinzelin, maître de verreries en bouteilles à Bouchain, près de Neuville-sur-Escaut (Nord), propose une solution plus élaborée : le « nouveau système de moules pour la fabrication des bouteilles appelé couramment moules à lumières » (brevet n° 154525 du 29 mars 1883). La particularité de ce moule métallique réside dans le fait qu'il présente un nombre déterminé d'encoches régulières dans lesquelles des morceaux de bois profilés s'insèrent mécaniquement lors de sa fermeture et se retirent de même à son ouverture, pour être plongés dans de l'eau. Le contact de la paraison et du bois humidifié (pour qu'il ne brûle pas trop vite) provoque un fartage automatique. Les « lumières » apparaissent donc à la fermeture et à l'ouverture du moule au travers des « fenêtres » des encoches. Plus simplement, Jules Henrivaux présente au début du XXe siècle « l'appareil à couper les plumettes [ou petits copeaux de bois] et à les introduire dans les moules à bouteilles »18. Le maître de verreries Wagret prend, lui, un brevet en 1903 pour « emploi de la sciure de bois en remplacement de la plumette employée dans les verreries à bouteilles et appareil distributeur de sciure de bois » (brevet n° 335274).
Pour souffler la paraison de verre chaud et malléable, le souffle humain est bientôt remplacé par celui de l'air comprimé. En effet, dès 1823, Ismaël Robinet, souffleur en cristal à Baccarat imagine de substituer son propre souffle à celui d'une pompe manuelle ressemblant presque à une pompe à vélo actuelle : la « pompe Robinet ». La puissance du souffle ainsi obtenu permet, dans la décennie qui suit, de souffler du cristal dans des moules complets « en plein », c'est-à-dire présentant un décor intérieur relativement complexe. En bouteillerie, un peu avant 1840, les frères Coutures de Bordeaux emploient des « réservoirs à vent » pour faire prendre forme aux bouteilles de leurs verriers dans des moules complets. Vers 1852-1855, le soufflage à l'air comprimé est utilisé à la verrerie de Vauxrot, mais devant la réticence de leur clientèle champenoise, les Deviolaine se bornent à n'employer ce moyen de formage que dans la production de bouteilles communes à destination de la capitale par exemple. Malgré bien des efforts, force est de constater que le remplacement du souffle humain par celui de l'air comprimé ne parvient pas à s'imposer en France. Pourtant, l'intérêt du procédé est évident puisqu'il permet de soulager l'homme pendant son travail et d'éviter la propagation de certaines maladies comme la tuberculose ou la syphilis. D'autres inventeurs proposeront leur solution, comme Léon Appert vers 1879, Mallet-Chassagny [de Lyon ?] en 1881 (brevet du 26 janvier, n° 140792, « appareil destiné à supprimer l'insuffisance buccale chez les ouvriers fabricants de bouteilles et de verre soufflé »), ou encore Brun en 1896 (brevet n° 253966 du 14 février, « canne à souffler le verre auto-souffleuse à l'aide d'un gaz liquéfié ou comprimé à de fortes pressions ou même d'un liquide injecté et vaporisé »)19.
Il reste cependant un problème : l'enfoncement de la piqûre. Dans les débuts de l'utilisation des moules fermés, le verrier devait encore intervenir manuellement pour réaliser l'opération. Grâce aux recherches incessantes des professionnels du verre, il va pouvoir laisser le fond de celle-ci se déformer dans un moule complémentaire en terre réfractaire présentant une pointe centrale. En effet, le 11 novembre 1876, Augustin Pailly, directeur de la verrerie à bouteilles de Lourches (Nord) prend un brevet pour « un système de moule à piquer les bouteilles ». Le 6 septembre 1879, Eugène Houtart, maître de verreries à Denain, réussit à mettre au point « un nouveau système de moule fermé tout en métal destiné à mouler et à repiquer les bouteilles avec le mode de travail ordinaire usité en France »20. La même année, Jules Tronchet présente lui aussi un moule complet dans lequel il est possible de former à la fois la bouteille et sa piqûre sans difficulté. Il est d'ailleurs rejoint par Petitjean en 1884 (cf. supra). Un an plus tôt, Émile Dahiez de Fresnes-sur-Escaut (Nord), déposait un brevet pour « une nouvelle disposition du fond des moules fermés dans lesquels s'opèrent le soufflage et le piquage des bouteilles »21. Chacun fait preuve d'imagination et, dans ce domaine, Claude Vernay y ajoute l'opiniâtreté. Ayant pris un premier brevet « pour moule à bouteilles avec sous-appareils, système Vernay » le 19 juillet 1880 (n° 187819), il ne cesse de perfectionner son invention22. Le 26 juin 1890, il dépose un nouveau brevet pour « moule à bouteilles et son appareil, système C. Vernay » (n° 206390)23. Enfin, il aboutit à la conception d'une « machine à fabriquer les bouteilles […] » en 1895 ; mais cela dépasse notre champ d'études24.
Tant qu'il n'existe aucune machine semi-automatique ou automatique de fabrication des contenants, le verrier perpétue des gestes immémoriaux. Une fois le corps de la bouteille soufflé, il doit détacher la pièce afin de la reprendre par le cul pour pouvoir réchauffer le haut du col et modeler définitivement la bague et la lèvre. Toutefois, lorsqu'il sépare l'objet de la canne de soufflage, il lui faut le poser sur une plaque (en terre réfractaire pour éviter les chocs thermiques) ou table appelée cachet. Cependant, ce geste peut provoquer la déformation du fût soufflé dans le moule de fond, par écrasement de la paroi sous l'effet du propre poids de la bouteille par exemple. En 1876, Henri Fox, employé de verrerie à Vauxrot, imagine le « cachet tournant, système Fox », appareil composé principalement d'une feuille de tôle demi-cylindrique à la dimension du fût de la bouteille et fixé sur une des bardelles du banc du verrier. Déposé dans celui-ci, le corps de la bouteille roule plus ou moins d'une extrémité à l'autre jusqu'à se stabiliser dans le creux. Le corps de la bouteille conserve donc sa forme cylindrique, d'autant mieux que le contact du métal dont est fait le cachet tournant vient « glacer », c'est-à-dire figer, la paroi externe de la bouteille25. Le système Tronchet de 1878 (cf. supra) comporte également un « cachet à glacer » demi-cylindrique. Sans risque, la bouteille peut être reprise pour être terminée.
Depuis toujours, pour effectuer cette dernière opération, l'officiant utilise un pontil, c'est-à-dire une canne ou un ferret (en fer creux ou plein) dont l'extrémité est enrobée de verre chaud qu'il vient coller sur le fond de sa bouteille. Le verre adhère, mais ne se soude pas véritablement. Au moindre choc sec, la pièce se détache. Il existe des pontils verre sur verre, en plein ou en anneau, mais également fer sur verre. Ce n'est que vers la fin des années 1840 que commence à être employé, en France comme en Angleterre, un pontil d'un nouveau genre : le sabot. En forme d'étrier ou de lanterne, sorte de boîte ronde à bords hauts pleins ou ajourés, le sabot métallique est fixé au sommet d'une grande tige de fer et permet de reprendre la pièce en se passant du pontil, dans la mesure où le diamètre du cul de la bouteille est respecté. Le gain de temps est considérable (fig. 5).
Fig. 6 a et b. Les anciens (a) et les nouveaux (objet du dépôt, b) fers à embouchures employés à Quiquengrogne en 1841 et figurant sur le dessin du brevet « des fers à piton octogones et plaques pour faire simultanément les bagues et les embouchures des bouteilles avec une grande régularité », déposé le 1er mai 1841 par Gustave Van Leempoël de Nieuwmunster et breveté le 22 mai suivant ; © Office de la propriété intellectuelle (Belgique).
Revenant au façonnage de la bouteille, une fois cette dernière reprise au pontil ou au sabot, il est désormais possible au verrier d'appliquer un fin filet de verre chaud, la cordeline (future bague) à l'extrémité du col et de réchauffer l'ensemble pour le rendre plus malléable. À la suite, l'homme modèle le sommet du col avec ses fers de verrerie, outil à deux lames métalliques parallèles. Mais à Sèvres au Bas-Meudon, il utilise un outil nouveau : les fers à embouchures. Celui décrit par les Encyclopédistes en 1772 permet à l'officiant de dresser le sommet de la lèvre du col tout en redressant l'axe de la cordeline. Puis en 1786, l'outil sévrien est perfectionné car l'ensemble cordeline et lèvre est conformé en un seul mouvement grâce à une sorte de poinçon d'embouchure, outil comportant une pointe centrale terminée par une lame concave qui sert à finir l'intérieur du col, et une pointe excentrée terminée par un poinçon présentant une profonde rainure dans laquelle sont rabattues les inégalités du verre de la cordeline qui est standardisée par ce moyen26. Cette innovation technique reste propre à l'établissement de Sèvres au Bas-Meudon et y sera même perdue sous la Révolution ou l'Empire27. Cependant d'autres verriers mettent au point une technique similaire. En 1841, Édouard Perrot mentionne l'utilisation « d'une espèce de tenaille avec une rainure verticale, qui exige quatre manipulations et ne produit que difficilement des embouchures de même dimension ». Puis il compare l'outil à l'invention de Gustave Van Leempoël de Nieuwmunster, maître de verreries à Quiquengrogne, composée « de deux fers à pitons octogones et d'une plaque, au moyen duquel l'embouchure est formée ainsi que la rainure en un seul mouvement, avec toute l'exactitude qui appartient à la mécanique ; [d'où une économie des] trois quarts du temps aujourd'hui employés » (fig. 6a et 6b)28. En fait, l'ancien outillage de Quiquengrogne comporte deux fortes lames métalliques de section carrée se terminant par une rainure intérieure à angles droits dans le creux de laquelle le verrier forme la bague. Grâce au nouveau système breveté en 1841, l'ouvrier, bloqué par la plaque fixée sur un piton octogonal central sur lequel se referment deux demi-mâchoires de conformation de la bague, ne peut plus « enfoncer le côté du fer plus ou moins avant dans le col de la bouteille » comme auparavant, ce qui avait pour effet de rendre « les embouchures irrégulières et exigeoit des bouchons de toutes dimensions »29.
Fig. 7 a, b, c. Fers à embouchures de 1856 en situation sur col de bouteille parisienne ; © O. Boilly, Musée d'histoire naturelle de Lille, inv. n° MI 7439/279.
Or, l'emploi de la « mécanique » d'embouchure à Quiquengrogne va générer une malfaçon au niveau du col des bouteilles si bien qu'en 1844, Van Leempoël abandonne son utilisation. Mais l'évolution technique se poursuit dans le nord de la France. Des fers à embouchures de conception plus aboutie par rapport aux précédents, sont utilisés par les verriers à bouteilles du Valenciennois. Vers 1856, Vancauwelaert et Wagret en font entrer un exemplaire dans les collections du Musée d'histoire naturelle de Lille (inv. n° MI 7439/279, fig. 7a, b et c). L'usage se répand. En décembre 1858, l'établissement de Quiquengrogne propose un échantillonnage à la veuve Clicquot-Ponsardin qui l'apprécie « parce que l'instrument avec lequel les quinze cents bouteilles ont été perfectionnées semble avoir fait disparaître, au moins en grande partie, le grave défaut » d'embouchure maintes fois signalé30. L'utilisation de cet instrument de calibrage s'étend à Trélon puisque nous le retrouvons à la verrerie Collignon et Fils deux ans plus tard, modernisé. En effet, le 29 août 1860, cette société prend un brevet « relatif à des perfectionnements apportés aux fers ou pinces de verrier » (n° 46488). Puis, le 12 décembre 1868, Collignon et son gendre Clavon apportent une nouvelle modification, laquelle permet cette fois « de déterminer d'une façon très exacte la saillie du cordon du col de n'importe quelle bouteille » (brevet n° 83545). Cela n'empêche pas Antoine Gromont, forgeron à Anzin, de déposer un brevet « pour un fer servant à faire les embouchures et les bagues des bouteilles » le 21 avril 187531. Ainsi que le fait remarquer Valérie Marchal, selon la loi française de l'époque, tout brevet est déposable puisque l'organisme officiel d'enregistrement ne se préoccupe pas des questions d'antériorité32.
Le sabot contenant la bouteille terminée est transporté par de jeunes porteurs à l'arche de recuisson à longueur de journée de travail. Aussi, soucieux d'alléger la peine de ceux qui sont le plus souvent de jeunes adolescents, Alain Chartier précédemment cité, explique en 1878 qu'il a fait remplacer le manche en fer plein par un manche en fer creux33. La masse à porter s'en trouve donc diminuée. Eugène Houtart (cf. supra) résout ce problème de pénibilité en prenant un brevet le 27 novembre 1879 « pour le transport mécanique des bouteilles et autres objets de gobletterie »34. Le 16 novembre 1896, la Société anonyme des Verreries de Dorignies présente un « système de transport mécanique des bouteilles et autres objets analogues du four à l'arche à recuire et de manipulation des cannes » (brevet n° 261349). Le 18 août 1900, Georges Chappuy, maître de la verrerie de Frais-Marais (près de Douai) mandate Émile Leclerc, ingénieur dessinateur, pour le dépôt de son invention : « un appareil destiné à assurer dans les verreries le transport des bouteilles et autres objets en verre à l'état incandescent depuis la place où ils sont façonnés jusqu'au four à recuire »35. Jules Henrivaux décrit, en 1903, le fonctionnement d'un transporteur mécanique dont il signale l'emploi à la verrerie Houtart de Denain36. Les Houtart demeurent à la pointe de la recherche : en décembre 1912, le « transporteur aérien » imaginé par Charles Houtart et en service à Denain comme à Dorignies, est présenté dans le Bulletin de la Société industrielle du Nord de la France. Un seul desservant réceptionne la fabrication de trois à quatre places de travail, d'où une économie de main-d'œuvre jeune peu qualifiée et un encombrement moindre, puisque chaque sabot circule sur un rail suspendu dans la halle. Semblable appareil est installé à la verrerie en bouteilles de Fourmies au début des années 1920, desservi par un « décrocheur », nouveau métier de verrerie qui disparaîtra bien vite avec la mécanisation.
Tout n'est pas écrit, puisque bien des innovations ont contribué à l'amélioration des conditions de travail du souffleur en bouteilles dans le nord de la France au XIXe et début du XXe siècle, lui permettant d'accroître sa cadence de fabrication et la qualité de ses pièces. Nous n'en avons fait état que d'une partie, la plus voyante, mais il serait judicieux d'en poursuivre l'énumération pour éclairer d'un jour différent la description du métier de verrier faite par les syndicalistes de la spécialité à partir des années 1890. Certes, le métier est dur, mais qu'en aurait-il été si le souffleur en bouteilles n'avait bénéficié de l'accumulation de toutes ces innovations techniques à son service pendant plus d'un siècle ? Car c'est bien de l'ensemble de ces nouveautés additionnées les unes aux autres, lentement, presque imperceptiblement, que découle au bout du compte l'amélioration de la production des contenants en verre et de sa productivité. L'innovation se dessine ici, non pas par une véritable rupture avec le passé, mais bien par un changement dans la continuité.
Stéphane Palaude
Gérard Caudrelier
- 1. ↑ Une partie des renseignements contenus dans cet article est issue du dépouillement des brevets industriels effectué par Caudrelier Gérard à l'Institut national de la propriété industrielle, tandis que l'autre partie provient de la thèse de doctorat en Histoire de Palaude Stéphane, 2009, Verreries noires d'Avesnois-Thiérache, XIXe-XXe siècles, Université Charles-de-Gaulle, Lille III (à paraître), et de recherches complémentaires réalisées par ce dernier aux Archives départementales du Nord (ADN) et à l'Office de la propriété intellectuelle (Belgique).
- 2. ↑ Diderot et d'Alembert, X, 1772, Recueil de planches, sur les sciences, les arts libéraux, et les arts méchaniques avec leur explication, Paris, Masson.
- 3. ↑ Lettre de Deviolaine & Cie, juin 1878 ; Archives Saint-Gobain à Blois (ASGB), Fonds Historique C 174.
- 4. ↑ Les Verreries de Denain à l'Exposition Universelle de Bruxelles, 1910, p. 8. Charneau A., 1886, Fours de verrerie à bassin continu chauffé au gaz avec accumulateur de chaleur, Paris, E. Bernard Cie, p. 2. Il s'agit d'un « four à bassin intermittent, 12 ouvreaux ». Charneau cite également « un four à bassin continu, 4 ouvreaux, et un four à bassin continu, 2 teintes, 8 ouvreaux » qu'il a installés à la verrerie de Frais-Marais (Nord).
- 5. ↑ Cf. réponse des maîtres de verreries E. Houtard et A. Wagret aux attaques du syndicaliste verrier Jaboulaye, parue dans le Réveil du Nord, 19 mai 1891, 3e année, n° 139.
- 6. ↑ Damour Emilio, 1936, Cours de verrerie, Troisième partie, Le refroidissement du verre, Le travail du verre, Propriétés physiques à froid, Paris, Libr. polytechnique Ch. Béranger éd., p. 214.
- 7. ↑ Henrivaux Jules, 1903, La verrerie au XXe siècle, Paris, Imp. Bernard, p. 196.
- 8. ↑ « Brevet pour un nouveau four de verrerie à bassin pour la production du verre à bouteilles et du verre à vitres » du 7 juillet 1885 ; Bour Pierre, « La machine Boucher : vers la mécanisation de la fabrication des bouteilles », in Bour Pierre (dir.), 1998, Claude Boucher, Les cent ans d'une révolution, Une histoire des industries verrières à Cognac, Musée de Cognac, Cognac, Imp. Presse du Temps, p. 31, note 8.
- 9. ↑ Voir le « schéma de la ventilation d'un four » de Baret J., 1926, « Note sur la ventilation artificielle des fours dans les verreries à soufflage mécanique », Bull. de l'Inspection du travail, nos 1 à 6, p. 323.
- 10. ↑ Des échantillons de fabrication de verre plat, dont certains cannelés, ont également été offerts par les mêmes maîtres de verreries au Musée d'histoire naturelle de Lille vers cette époque, ainsi que par la verrerie Renard père et fils, de Fresnes-sur-Escaut (Nord). Voir Vandecasteele Dominique, « Les collections techniques autour du musée d'histoire naturelle de Lille », in Moinet Eric (dir.), 2007, Transparences, Histoire du verre et du cristal en Lorraine, catalogue d'exposition, Nancy, Musée Lorrain, 6 octobre 2007-7 janvier 2008, Serge Domini éd., p. 60-61.
- 11. ↑ Verrerie Bouteilles de Sèvres, 1820, petite assiette de porcelaine dure peinte par L. Develly ; Musée national de la céramique à Sèvres. Le mamelon n'existe pas sur les bouteilles du XVIIIe siècle et n'apparaît pas non plus sur les dessins de Dioncq-Lenglé ou de Jullien représentant dans le détail des bouteilles en 1809 ; cf. dessin accompagnant la réponse de Dioncq-Lenglé, maître de la verrerie de Dunkerque (Nord), à l'enquête préfectorale de 1809 et « Dessin de l'aérifère de M. Jullien de février 1809 », respectivement ADN, M 581/228 et Bull. de la Soc. d'encouragement pour l'industrie nationale, 1809, vol. 8, p. 58-59. La bulle voit le jour au fond de la piqûre de la bouteille au moins après 1810, mais plus probablement vers 1835-1840. L'utilisation d'une molette à tête creuse permet alors un meilleur centrage de la piqûre par le biais de la bulle.
- 12. ↑ Cf. lettre du 30 juin 1878 d'Augustin Pailly, maître de verreries à Lourches (Nord), aux membres du jury de l'exposition universelle de 1878 ; ASGB, Fonds Historique C 174.
- 13. ↑ ADN, M 578/13.
- 14. ↑ Henrivaux Jules, op. cit., p. 166.
- 15. ↑ Ibid., p. 169. L'auteur signale aussi l'utilisation de moules tournants − dont il ne précise pas le type − à la verrerie de Folembray (Aisne) vers la fin du XIXe siècle, lesquels y sont toujours employés lors de la sortie de son ouvrage en 1903 ; ibid., p. 166.
- 16. ↑ Ce dernier est le gérant de la verrerie en bouteilles de La Neuvillette-les-Reims (Marne).
- 17. ↑ C'est pour cette raison qu'assez souvent dans l'iconographie représentant l'intérieur d'une halle aux fours à bouteilles dans le nord de la France, nous pouvons remarquer, par exemple, la présence d'une sorte de distributeur de brins de paille à proximité du moule de soufflage.
- 18. ↑ Henrivaux Jules, op. cit., p. 205-206.
- 19. ↑ Concernant Léon Appert, voir Carré Anne-Laure, « Léon Appert, innovateur verrier, entre brevets et valorisation des collections », communication au présent colloque de Nancy des 26-28 mars 2009.
- 20. ↑ ADN, M 571/30 (Pailly) et M 571/32 (Houtart). Eugène Houtart prend un nouveau brevet le 14 août 1882 « pour un système de moule-fermé à bouteilles » ; ADN, M 571/32.
- 21. ↑ Le 1er septembre 1883 ; ADN, M 571/33.
- 22. ↑ Certificats d'addition des 18 juillet 1881 et 9 août 1882 pris à Lille (Nord) ; ADN, M 571/32.
- 23. ↑ Claude Vernay est alors déclaré comme étant comptable à Armentières (Nord) ; ADN, M 571/35.
- 24. ↑ Jules Henrivaux mentionne que la machine Vernay « fut essayée […] à Lyon dans les premiers mois de l'année 1894 [sans résultat], à Folembray [sans plus de succès, et enfin] plusieurs mois à la Verrerie de Denain en 1895, sans qu'il eût été possible d'obtenir un embryon de bouteille » ; Henrivaux Jules, op. cit., p. 168. En dépit des très mauvais résultats relatés par cet auteur, Claude Vernay n'en dépose pas moins un brevet pour une « machine à fabriquer les bouteilles et autres articles en verre » le 31 décembre 1895 (n° 252894). Il poursuivra ses recherches et prendra un nouveau brevet de « machine multiple pour la fabrication automatique des bouteilles et autres objets en verre » le 28 janvier 1901 (n° 307537).
- 25. ↑ Brevet n° 114959 du 16 octobre 1876.
- 26. ↑ Voir Palaude Stéphane, 2006, « « Divine bouteille, souffle humain, savoir encyclopédique », Éclats de Verre, La revue de généalogie des Verriers d'Europe, n° 7, mai, p. 18-20.
- 27. ↑ Au moment de la rédaction de sa thèse de doctorat en Histoire, Stéphane Palaude ne connaît pas l'existence de l'invention de Gustave Van Leempoël de Nieuwmunster, de Quiquengrogne, présentée ci-après. Il considère simplement que l'emploi des fers à embouchures sévriens n'a pas eu de développement en-dehors de l'établissement de Sèvres au Bas-Meudon, voire même y a disparu au début du XIXe siècle. Sur ce dernier point, cet avis n'a pas changé. En revanche, la diffusion des fers à embouchures a peut-être eu lieu durant le premier tiers du XIXe siècle ou, plus vraisemblablement, des recherches similaires effectuées par d'autres verriers durant cette période ont abouti à la création et la diffusion des fers à embouchures, comme à Quiquengrogne par exemple.
- 28. ↑ Perrot Edouard, 1841, Revue de l'exposition des produits de l'industrie nationale en 1841, Bruxelles, chez l'auteur, p. 171-172. Cet « instrument (composé de deux pièces) propre à faire simultanément les bagues et les embouchures des bouteilles […] a été breveté [par Gustave Van Leempoël de Nieuwmunster] par arrêté royal [belge] du 22 mai 1841 » ; Catalogue des produits de l'industrie belge à l'exposition de 1841, 1841, 2e éd., Bruxelles, Société typographique belge, p. 46.
- 29. ↑ Brevet Gustave Van Leempoël de Nieuwmunster du 22 mai 1841 concernant « des fers à piton octogones et à plaques pour faire simultanément les bagues et les embouchures des bouteilles avec une grande régularité ».
- 30. ↑ Lettre de 3 décembre 1858 ; Archives Veuve Clicquot-Ponsardin, Livre de copies de lettres, 1858.
- 31. ↑ ADN, M 571/30.
- 32. ↑ Voir Marchal Valérie, « Brevets, marques et modèles, XIXe-XXe siècle », communication au présent colloque de Nancy des 26-28 mars 2009. £LIEN£
- 33. ↑ Note sur la société Alain Chartier & Cie du 19 juin 1878 ; ASGB, Fonds Historique C 174.
- 34. ↑ ADN, M 571/32.
- 35. ↑ Ce dépôt est assorti d'un certificat d'addition le 1er octobre suivant ; ADN, M 571/38.
- 36. ↑ Henrivaux Jules, op. cit., p. 201-203.