Chimie industrielle et innovations dans les compositions verrières, fin XVIIIe-XIXe siècle
Marie-Hélène Chopinet
UMR 125 CNRS/Saint-Gobain, Aubervilliers (France).
Les méthodes de sélection des matières premières étaient encore très empiriques à la fin du XVIIIe siècle, faute de compréhension de leur nature chimique, de celle des impuretés qu'elles contenaient et de la chimie du produit issu du processus de fusion, le verre. L'évolution des matières premières alcalines dans les mélanges vitrifiables est particulièrement représentative de l'influence de la chimie industrielle à partir de la fin du XVIIIe siècle. Après la purification de la soude naturelle rendue nécessaire par les exigences du marché pour un verre plus blanc, la révolution française et les événements qui ont suivi accélérèrent la transition vers un carbonate de sodium synthétique produit par le procédé Leblanc durant le XIXe siècle. Le coût de cette matière première industrielle encouragea les fabricants de verre colorés comme le verre à bouteille à recourir soit aux anciennes matières premières impures, soit à des mélanges de chlorure de sodium et de sulfate de sodium, ce dernier étant le précurseur du carbonate de sodium dans le procédé Leblanc. Le sulfate de sodium lui-même fut largement utilisé dans les usines produisant du verre plat dès qu'on eût compris que la coloration apparaissant dans le verre était due au fer présent à l'état d'impureté. Tout aussi importante fut la découverte que la réaction entre sulfate de sodium et silice était possible directement dans le four verrier si l'on ajoutait du charbon au mélange vitrifiable. Sous une forme un peu différente, ce processus fut à l'origine d'une méthode d'affinage et de brassage du verre fondu susceptible de remplacer l'utilisation de l'arsenic déjà identifié comme un produit toxique. L'invention du procédé Solvay à la fin du XIXe siècle rendit la production du carbonate de sodium moins onéreuse. Le remplacement de toutes les formes de matières premières alcalines par ce nouveau produit intervint avant la fin de la première moitié du XXe siècle, bien qu'une partie du sulfate de sodium ait été conservée dans le mélange vitrifiable après vérification de son utilité pour l'affinage du verre.
Evolution in alkalis raw materials: salt-flux in glass compositions during the 18th century.
At the end of the 18th century, sorting raw materials was still very much empirical, as the chemical nature, the range of impurities and the chemicals process at work during fusion were not understood. Evolution of alkalis raw materials is a good example of the influence of the application of chemistry in industry at the end of the 18th century.
At first the desire for a clearer glass induced a purification of soda, but after the upheavals during the French revolution, transition towards the use of sodium carbonate made with the Leblanc process was accelerated. The high cost of this « new » raw material encouraged bottle glass producers (using coloured glass) to go back to old non purified materials or to use a mix of sodium carbonate and sodium sulfate, the later being a first step in the Leblanc process. Sodium sulfate was extensively used in plate glass production as soon as it became known that the glass coloration was due to iron oxide particles. The discovery that the chemical process at work between sodium sulfate and silica in the furnace was improved by the introduction of coal to the batch was also very important.
In a slightly different way this process was also used as a method to refine and stir the molten glass, it was identified as a remedy against the use of arsenic, already characterized as a toxic agent. Solvay's innovation at the end of the 19th century made the production of sodium carbonate less expensive. The replacement of all other alkalis by the Solvay soda was well under way before the second half of the 20th century. Sodium sulfate however was still used in the batch as it helped refining.
Introduction
Comme les autres verriers, selon Turgan (Tome 3, p 22) :
Les premiers fondateurs de Saint-Gobain eurent presque tout à créer (…) et avaient de plus à lutter contre leur ignorance absolue en fait de chimie. Ils allaient au hasard, un peu comme les marchands de nitre de Pline qui, traversant la Phénicie et s'étant arrêtés sur les bords du fleuve Belus, découvrirent le verre en faisant chauffer leur marmite sur des morceaux de nitre (natron) au lieu de chenets : mêlé au sable du désert, le nitre se fondit, fit un liquide transparent, et de là le verre. Ils s'épuisaient en dissertations sur l'alkali végétal et sur l'alkali minéral, dont ils ne connaissaient pas la composition plus de l'un que de l'autre. Ils craignaient beaucoup le sel de verre qui se formait dans la fabrication. Ce sel renfermait du sel fébrifuge de sylice (sic), du tartre vitriolé, etc. Le mélange de sable, de soude et de manganèse avec lequel ils préparaient une première composition appelée fritte, était le secret de tradition de quelques vieux contremaîtres de la maison.
Le développement des connaissances en chimie a permis de fiabiliser et d'affiner la composition chimique du verre et le choix des matières premières : l'un des exemples les plus frappants est celui du fondant, le « porteur d'alcalin ». Son évolution de la fin du XVIIIe siècle jusqu'au début du XXe est marquée par plusieurs changements spectaculaires dans lesquels les avancées de la science et l'imagination des verriers ont collaboré de façon remarquable. Ces avancées, que nous allons décrire – et d'autres, évidemment – ont d'ailleurs conduit à une évolution également considérable du prix du verre durant cette période, au point qu'en 1897, J. Henrivaux, ancien directeur de Saint-Gobain pouvait écrire : « Le carreau de papier commence à être inconnu dans nos villages, et l'estampe encadrée sous un verre remplace, dans la demeure du paysan, l'image grossière collée à la muraille. »
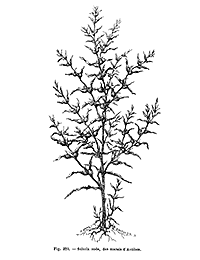
Fig. 1. Salsola Soda des marais d'Antibes, une des plantes marines calcinées pour obtenir la soude, d'après Figuier.
XVIIIe siècle
La soude auDes produits naturels
Avant la révolution française, le carbonate de sodium, la soude, était le résultat de la calcination de plantes marines contenant le sodium sous des formes diverses : tartrate, oxalate, chlorure… Le terme de soude, encore fréquemment utilisé aujourd'hui pour désigner le carbonate de sodium, provient du nom d'une famille de plantes permettant d'obtenir le produit, les « soda » (fig. 1). Par exemple, en Europe, les meilleures soudes provenaient d'Espagne. On les appelait barilles car elles étaient obtenues par calcination de la salsola soda appelée barilla.
De qualité variable
La teneur de ces soudes en carbonate de sodium était évidemment très fluctuante. L'analyse étant impossible, le verrier avait en général une recette pour juger de la qualité du produit.
À ces moyens (la couleur) de juger les soudes à l'inspection, on joint le secours de l'odorat et du goût : il faut que, mises sur la langue, elles soient lixivielles sans être salées. On recherche une causticité franche et piquante sans amertume ; enfin on met un peu de salive sur un morceau de soude pour juger s'il ne se développe pas d'odeur hépatique qui dénote des sulfures, signes d'une soude de mauvaise qualité (G. Bontemps p. 54).
Les impuretés ordinaires contenues dans cette matière première naturelle étaient des sels alcalins solubles à l'eau comme le sulfate ou le chlorure, des sels de calcium et de magnésium insolubles (les « matières terreuses ») et du charbon provenant de la calcination.
Le charbon se trouvait intentionnellement ou non éliminé par le frittage du mélange vitrifiable, opération qui précédait la fusion proprement dite et qui avait comme autre conséquence la déshydratation et la décarbonatation plus ou moins complète du mélange, d'où un gain en temps de fusion et une amélioration de la durée de vie des installations.
Composés | Poids % | Sans eau | |
---|---|---|---|
Partie soluble dans l'eau | Carbonate de soude (alcali minéral) | 25 | 33,7 |
Sulfate de soude (sel de Glauber) | 4.17 | 5.6 | |
Chlorure de sodium (alcali marin) | 2.22 | 2.9 | |
Carbonate de potasse (alcali végétal) | 3.36 | 4.5 | |
Sulfate de potasse (tartre vitriolé) | 2.11 | 2.8 | |
Partie terreuse | Carbonate de chaux | 11.48 | 15.5 |
Magnésie | 2.20 | 2.9 | |
Insoluble dans l'eau | Alumine | 2.28 | 3.0 |
Silice | 6.24 | 8.4 | |
Charbon | 14.96 | 20.2 | |
Eau et perte | 25.98 |
Table 1. Analyse d'une bonne soude selon Bontemps.
Une première étape, la purification de la soude
Dès 1758, Pierre Delaunay Deslandes, nouveau directeur de l'usine de Saint-Gobain entreprit la purification de la soude par extraction des sels solubles à l'eau, donc alcalins. Il obtint ainsi une matière première beaucoup plus stable qui améliora notablement la qualité de sa production de glace. Il est remarquable qu'il se soit rendu compte que parallèlement à cette modification, il fallait ajouter au mélange vitrifiable de la chaux qu'il savait être l'oxyde dominant dans la partie insoluble (H. de Coqueréaumont p. 253) : « On se servait de chaux dans la fabrication des glaces sans s'en douter ; on ne faisait pas attention que la soude en nature contenait plus de moitié de matières terreuses qui après avoir passé un temps considérable dans les fours à frittes avaient acquis la propriété de la chaux » (Delaunay-Deslandes).
La méthode expérimentale de Deslandes est intéressante (H. de Coqueréaumont p. 253) : « Il prit du marc de soude lessivé, le fit fritter pour le décolorer, fit des compositions comparatives avec cette fritte et avec de la chaux, et constata que le résultat était le même. » Le test permettant de comparer était probablement l'ouvrabilité du verre, la viscosité du liquide dépendant fortement de sa composition chimique.
« Allant plus loin, il essaya la pierre avec laquelle on faisait la chaux, c'est-à-dire le calcaire et ne trouva aucune différence. Il ne dit pas pourquoi, arrivé à ce point, il n'a pas persévéré dans cette voie et adopté définitivement le calcaire de préférence à la chaux. Il est probable que les fours chauffant moins que les nôtres, il fallait leur donner un élément tout préparé plutôt qu'un produit à décomposer. » Un peu plus tard, Deslandes s'aperçut que le mélange non fritté fondait aussi bien et il supprima l'opération de frittage.
Ce texte très intéressant met en évidence le processus expérimental par essais et comparaison utilisé à cette époque en l'absence de tout moyen analytique, mais révèle aussi que Deslandes avait bien en tête les connaissances de ce temps en chimie : solubilité à l'eau des sels alcalins en général, filiation entre CaCO3, CaO et Ca (OH)2, même s'il n'avait pas les outils pour expliciter les réactions.
Les verriers faisaient donc face à un gros problème de régularité dans l'approvisionnement en fondant. Outre le problème de la stabilité de l'approvisionnement, l'importation des soudes d'Espagne coûtait très cher aux entreprises françaises en général. En fait, dès 1775, l'Institut proposa un prix pour récompenser celui qui arriverait à transformer le sel marin en carbonate de soude, sans que ce prix puisse être remis faute d'inventeur.
Le problème posé par l'approvisionnement en « fondants » se trouvait donc posé depuis de nombreuses années, depuis toujours peut-être, pour des raisons technique, la qualité des produits du marché, et économique, leur prix.
la soude artificielle
Un coup de pouce de l'histoire, la révolution française :Après comme avant (les prix proposés par l'Académie des Sciences de Paris), la France donna chaque année à l'Espagne 20 à 30 millions de francs pour la soude que celle-ci lui fournissait. La guerre de la révolution étant survenue, l'importation de la soude et de la potasse fut empêchée et toute la potasse que la France produisait était immédiatement consommée par les fabricants de salpêtre et de poudre. Ce fut seulement alors que l'on connut et que l'on apprit à mettre en pratique le moyen de préparer la soude d'une manière avantageuse avec le sel marin ou le sel gemme. Le Comité de Salut Public décréta en 1793 que les indications les plus exactes lui soient communiquées sur toutes les fabriques de soude (R. Wagner tome 1, p. 371).
Selon P. Flamm (p. 28), « La science, autrefois le nourrisson de l'empirisme, devenue majeure, paya largement ses dettes ; car l'appel fait aux savants n'a pas été stérile. La chimie avait reconnu que le sel marin, si répandu à la surface du globe, était un composé de deux corps simples, du chlore uni à la soude ; il était donc naturel que les recherches se portassent vers ce sel si abondant dans la nature, afin de trouver un procédé économique qui permît d'en isoler la soude. »
Un inventeur malchanceux, Nicolas Leblanc
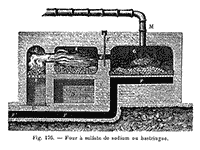
Fig. 2. Four servant à la fabrication du carbonate de sodium à partir du sulfate de sodium, d'après Figuier.
Dès 1791, Nicolas Leblanc (1753-1806), soutenu par le duc d'Orléans, avait mis au point un procédé de fabrication de la soude artificielle et l'usine de Saint-Denis fonctionna jusqu'en novembre 1793, date à laquelle le duc d'Orléans périt sur l'échafaud. Ses biens furent mis sous séquestre et l'usine dans laquelle il avait la plus grande part de propriété se trouva comprise dans le séquestre, la fabrication arrêtée et le matériel vendu. Lors de l'annonce de l'appel du Comité de Salut Public, Leblanc autorisa la publication de son procédé, jusque-là tenu secret. La seule rétribution de Leblanc et de ses associés fut la restitution de l'usine de Saint-Denis mais sans aucun moyen financier pour remonter la fabrication. Fatigué de ses tentatives pour obtenir justice, dans la misère, Leblanc finit par se suicider le 16 janvier 1806. Le procédé Leblanc est le suivant, selon P. Flamm (p. 30) (fig. 2) :
Les soudes artificielles sont composées de soude caustique, de carbonate de soude, de sel marin, de sulfure de chaux avec excès de base, ou plutôt de sulfure de calcium uni à la chaux et de carbone. Elles s'obtiennent en calcinant ensemble une certaine quantité de sulfate de soude, de charbon et de craie ; (...) On en fait un mélange exact ; on le jette dans un four à réverbère, dont la forme est elliptique et dont la température est un peu plus élevée que le rouge cerise, et on brasse ce mélange de quart d'heure en quart d'heure. Au bout d'un certain temps, la matière devient pâteuse ; alors on la pétrit bien avec un ringard en fer, puis on la retire et on la reçoit dans une chaudière. Cette matière est la soude artificielle
Pendant les guerres de la révolution, l'industrie française était paralysée par l'absence des soudes d'Espagne et l'invention de Nicolas Leblanc fut son sauveur (L. Figuier, préface) :
La fabrication des savons, celle du verre et toutes les branches secondaires qui se rattachent à ces deux troncs industriels, étaient suspendues ou anéanties ; les pertes subies par le commerce français étaient énormes. Un chimiste parut, et créa en France l'admirable industrie de la soude factice. Il serait presque impossible d'évaluer exactement les sommes immenses dont l'industrie a bénéficié par la découverte de Nicolas Leblanc, qui a permis d'extraire manufacturièrement la soude du chlorure de sodium contenu dans les eaux de la mer. D'où Nicolas Leblanc avait-il fait sortir les incalculables richesses dont il dota l'Europe ? De l'application d'un fait de chimie dont l'annonce n'aurait pas tenu quatre lignes dans un journal scientifique du temps, à savoir, la décomposition du sel marin par la craie, à une température élevée.
La soude artificielle brute, plus riche en carbonate de sodium que les diverses soudes d'origine naturelle mais contenant des impuretés gênantes comme le sulfure de calcium, fut d'abord utilisée seulement en verre à bouteilles et en verre à vitre. Cependant, les producteurs arrivèrent très vite à la purifier (fig. 3) et obtinrent un produit contenant d'abord 70 à 75 % de carbonate de sodium, puis jusqu'à 95 à 97 % en 1868 (G. Bontemps p. 57).
En 1810, la fabrication de la soude artificielle suffisait à tous les besoins de l'industrie française : un décret en date du 11 juillet prohiba l'entrée des soudes étrangères en France. À cette même date, la Compagnie de Saint-Gobain, faute de trouver un approvisionnement en rapport avec ses exigences, se décida à fabriquer elle-même sa soude, sur le site de Charles-Fontaine acheté pour cela. En 1823, la soudière fut transférée sur le site de Chauny (fig. 2 et 3).
le chlorure de sodium ?
Pourquoi pas le sulfate de sodium ou bien même,Un des inconvénients du procédé Leblanc était son coût. Les verriers envisagèrent l'utilisation des précurseurs du carbonate de sodium, le sulfate de sodium et même, pourquoi pas, le chlorure de sodium. En 1810, Clément Desormes de la Compagnie de Saint-Gobain prit même deux brevets1 dans ce domaine, l'un utilisant le sulfate de soude et le muriate de soude (chlorure de sodium) et l'autre uniquement du chlorure de sodium. Selon H. de Coqueréaumont, « la vérité est que les essais exécutés n'ont donné aucun bon résultat ».
Comment fondre avec du sulfate de sodium comme fondant ?
En fait, il est quasiment impossible de vitrifier le sable avec du chlorure de sodium. Le sulfate de sodium n'est pas non plus aisément un bon « fondant » : il ne se combine pas avec la silice, contrairement au carbonate de sodium, il flotte sur le bain de verre fondu et devait être retiré des pots soit par pochage soit par volatilisation ce qui prenait du temps et pouvait même se révéler dangereux s'il entrait en contact avec l'eau.
Donc, au tout début du XIXe siècle les verriers ne savaient pas utiliser ce produit. En outre, les fabricants n'avaient pas le droit de le vendre, au moins en France : le gouvernement craignait en effet que l'on ne puisse en extraire du chlorure de sodium (le sel) qui était fortement taxé.
La solution consista à mettre en contact directement dans le four verrier les composés intervenant dans le procédé Leblanc. En 1813, le chimiste allemand Gehlen précisa comment utiliser le sulfate directement dans les fours en le mélangeant avec du calcaire, du charbon et du sable : « pour 100 de silice, on emploie généralement de 33 à 40 de sulfate de soude, de 20 à 40 de carbonate de chaux ou la quantité de chaux équivalente, de 1.65 à 2 d'anthracite pilé, ou de 2.30 à 2.80 de braise de bois. » (G. Bontemps p. 59).
Le problème « fiscal » fut également enfin résolu :
La preuve ayant été rendue bien évidente que le sel marin produit avec du sulfate de soude serait bien plus dispendieux que le sel marin frappé alors d'un droit élevé, le gouvernement se décida enfin, en 1824, à lever les entraves qu'il avait mises à la vente du sulfate de soude, qui fut d'abord employé à la fabrique de verre à vitre de Prémontré (Aisne), et toutefois, on commença par fritter le mélange que l'on faisait de sable, sulfate, craie et charbon. Son emploi ne tarda pas à s'introduire dans toutes les autres fabriques de verre à vitre, et même de verre demi-blanc pour gobeleterie. (G. Bontemps p. 58)
Peut-on résoudre ce problème ?
Pourquoi les glaces au sulfate sont-elles plus colorées ?L'application au verre à glace, un verre de luxe, fut plus longue du fait des exigences de la clientèle en matière de caractéristiques optiques. Selon G. Bontemps (p. 59), en 1868 :
Quoique théoriquement on dût penser que le sulfate de soude décomposé par la craie et le charbon dans le creuset devait produire un verre aussi blanc que le carbonate de soude, tel n'était pourtant pas le résultat pratique obtenu, et les chimistes s'imaginaient que la légère teinte vert-bleuâtre du verre composé avec le sulfate pouvait être attribuée à une réaction d'une partie du charbon2 sur la soude. M. Gay-Lussac lui-même, qui présida longtemps le conseil de la manufacture de Saint-Gobain, était persuadé que pour cette raison on ne pourrait pas substituer le sulfate au carbonate dans la fabrication des glaces.
C'est à M. Pelouze que revient l'honneur d'avoir détruit cette erreur ; [à partir de 1850] partant de cette conviction profonde que de la silice, du sulfate de soude, de la chaux et du charbon, tous chimiquement purs, devaient produire un verre blanc, il reconnut bientôt que la coloration vert-bleuâtre constamment obtenue n'était due qu'à la présence de l'oxyde de fer, dont une infime proportion produit ce résultat, et comme le sable et la chaux employés à Saint-Gobain sont exempts de fer, c'est vers le sulfate de soude qu'il dut porter ses recherches, et c'est là, en effet, qu'il découvrit la proportion d'oxyde de fer qui suffisait pour produire la coloration que l'on ne pouvait, jusqu'à lui, éviter qu'en employant le carbonate de soude.
Le sulfate de soude contient généralement un léger excès d'acide sulfurique qui agit sur l'argile du creuset. Cette argile contient de l'oxyde de fer : voilà une cause de coloration, quoique sans doute très légère, mais c'est surtout de la sole en fonte du four dans lequel on décompose le sel marin par l'acide sulfurique (fig. 4) que provient l'oxyde de fer dont le sulfate de soude contient toujours une proportion plus ou moins notable. M. Pelouze, ayant par une opération subséquente amené le sulfate à un très grand état de pureté, l'a entièrement substitué au carbonate de soude dans la fabrication des glaces de Saint-Gobain, et a, par ce fait, apporté une très importante économie qui a permis de baisser beaucoup le prix des glaces.
Le coût des matières premières était de 2,06 F en 1868 contre 4,63 F/m2 auparavant, le carbonate de sodium coûtant 5 fois plus cher que le sulfate.
En bouteillerie, du sel ajouté à du sulfate
Durant la révolution française, le sel marin n'étant plus taxé, les fabricants de bouteilles, toujours à la recherche d'économies de matières premières, en utilisèrent avec du sulfate de sodium. Le procédé incluait un chauffage préliminaire (la fritte) de tout ou partie du mélange et il semble que l'eau incorporée était suffisante pour provoquer la réaction entre chlorure de sodium et silice qui est difficile à haute température.
Quand le sel marin fut de nouveau taxé, « les fabricants de bouteilles ont obtenu de l'État qu'on fît pour eux un sel demi-décomposé, c'est-à-dire contenant environ moitié sulfate, moitié chlorure de sodium, qui leur est ainsi livré à bien meilleur marché que le sulfate pur et s'emploie avec avantage dans la fabrication des bouteilles. » (G. Bontemps p. 62). Ce produit fut utilisé jusqu'à la nouvelle génération de fours, les fours à bassin et régénérateurs Siemens qui étaient trop rapidement corrodés par les chlorures.
Une nouvelle et dernière évolution : le procédé Solvay
Le procédé Leblanc fournissait du carbonate de sodium à un prix relativement élevé, de sorte que les chimistes poursuivirent leurs efforts pour trouver un nouveau procédé plus économique. Le procédé à l'ammoniaque était théoriquement connu depuis 1811 mais la mise au point d'une installation industrielle économique se révéla ardue. Il fut utilisé pour la première fois industriellement en 1865 par E. Solvay à Couillet en Belgique. Dans ce procédé le sel marin est traité par l'ammoniaque puis par CO2, produit par décarbonatation du calcaire, en formant du bicarbonate de sodium et du chlorure d'ammonium. Par chauffage le bicarbonate donne du carbonate de sodium. Un des avantages de ce procédé comparé au précédent réside dans le recyclage de l'ammoniaque produit, par réaction du chlorure d'ammonium avec du calcaire.
Où l'on découvrit les avantages du sulfate de sodium
Bien que ce nouveau procédé ait fourni du carbonate de sodium bien meilleur marché que l'ancien procédé Leblanc, la substitution du sulfate de sodium par le carbonate fut très longue en verrerie : des essais de substitution partielle du sulfate par du carbonate avaient eu lieu à partir de 1887 dans les usines de Saint-Gobain, sans grand succès.
Il semble qu'un des intérêts du sulfate résidait dans deux particularités dont l'une est la séparation du sulfate liquide du liquide silicaté dans les pots à haute température : les grains de sables résiduels, eux aussi moins denses que le silicate, se trouvaient alors en contact avec le sulfate et étaient ainsi digérés dans le verre.
Il y avait grande difficulté à affiner complètement les pots au carbonate et on n'obtenait qu'un verre incomplètement fini et vraisemblablement peu homogène à cause du maclage nul ou insuffisant. Cette absence d'homogénéité de la pâte composée de silicates de compositions différentes, devait s'accompagner d'une inégalité de la température et ces deux raisons peuvent expliquer la mauvaise liaison du verre et le feuilletage. (H. de Coqueréaumont p. 293)
Un autre intérêt des verres au sulfate est leur activité chimique à haute température : elle se traduit par une libération de gaz utile à l'homogénéisation. Ce dégazage se produit soit lors d'une élévation de température par réduction spontanée du sulfate en sulfite, soit, à plus basse température, moyennant un « maclage » avec une tige de bois ou une pomme de terre, en tout cas, un élément réducteur qui produit le même résultat. On obtient un moussage vigoureux conduisant à une bonne homogénéité du pot et à l'affinage du verre liquide, mais qui présente également des inconvénients du point de vue des installations. Le maclage n'était pas employé partout avec la même intensité ; certaines usines l'employaient comme adjuvant, sans diminuer beaucoup l'action de la chaleur ; d'autres, au contraire, et surtout celles qui ont des pots peu résistants, chauffaient très peu et maclaient énergiquement, l'utilisation du « macloir » provoquant la réduction chimique du sulfate et un dégazage suffisant sans que l'augmentation de température soit nécessaire.
Un moussage trop violent conduit à une usure accélérée des pots et les verriers ont toujours cherché à obtenir le même effet sans chauffer trop haut ou même sans moussage. Il s'est avéré que le « travail » du verre était hélas indispensable à l'homogénéisation.
Remplacement définitif mais partiel du sulfate par le carbonate : des avantages incontestables à l'usage
L'avantage économique du carbonate Solvay ne permit plus d'éluder la question au début du XXe siècle. « En 1906, à l'usine de Montluçon de la Compagnie de Saint-Gobain, on fit des essais de marche au carbonate, et l'on en conclut que le verre au carbonate ne s'affinait pas à la température ordinaire des fours, qu'en ajoutant une faible proportion de sulfate de soude ou de sulfate de chaux, il s'affinait et que l'acide sulfurique semblait avoir une certaine influence sur le travail du verre. » (H. de Coqueréaumont p. 295).
Cependant, en 1922 encore, par exemple, la Society of Glass Technology connut d'âpres discussions sur les avantages et inconvénients de l'utilisation comparée du sulfate et du carbonate de sodium en tant que constituant des mélanges vitrifiables (General Discussion, Society of Glass Technology). « Le verre à vitre fabriqué avec du carbonate de sodium est-il inférieur à celui qui est fait au sulfate ou bien moins facile à prélever ? » « Le mélange contenant au moins une part de sulfate de sodium est préférable, simplement parce que le verre, bien qu'étant légèrement moins fluide, a apparemment un palier de travail légèrement plus long. »
Un des membres de la Société indiqua très justement qu'il pensait que « la tendresse du verre était étroitement liée à son homogénéité. On pouvait donc obtenir un plus haut degré d'homogénéité avec le sulfate de sodium qu'avec le carbonate de sodium. Un verre vraiment homogène pouvait être soufflé plus facilement et pour cette raison on le disait tendre. »
Malgré toutes ces discussions dans le milieu verrier, en 1927, W.E.S. Turner pouvait dire que la tirée des fours avait fortement augmenté, d'un facteur 3 pour certains depuis 1916, et que c'était en partie dû à la substitution du sulfate de sodium par du carbonate et à l'accélération de la fusion de 40 %.
Cela n'échappa pas aux verriers : le résultat fut le mélange vitrifiable au carbonate de sodium, additionné de sulfate de sodium afin d'améliorer l'homogénéisation du verre, que nous utilisons encore aujourd'hui.
Conclusion
L'évolution des matières premières alcalines en verrerie au cours du XIXe siècle est assez représentative de celle de la chimie en général et de la chimie industrielle en particulier. La compréhension plus fine des réactions, liée à l'identification/séparation des éléments chimiques, à une nomenclature plus rationnelle et aux nouvelles méthodes d'écriture des réactions, a permis l'explosion de la chimie « lourde » de synthèse des produits de base, comme le sulfate de sodium ou le carbonate de sodium.
Les verriers n'ont d'ailleurs pas hésité à utiliser ces produits, voire à s'impliquer directement dans leur fabrication, leur but étant de satisfaire une clientèle de plus en plus exigeante et de plus en plus vaste, et de diminuer les coûts.
De nombreuses autres découvertes du XIXe siècle ont eu une influence majeure sur la verrerie : l'invention du four à bassin et à régénérateur des frères Siemens, l'invention du pyromètre et du thermocouple.
On constate également l'impact accélérateur d'un bouleversement de l'histoire comme la révolution française, tout comme le phénomène de la mécanisation du début du XXe siècle est fortement lié à la première guerre mondiale.
Marie-Hélène Chopinet
- 1. ↑ Brevets n° 565 et 566 du 18 juin 1810.
- 2. ↑ Par addition involontaire de carbone dans le mélange vitrifiable, on obtient en effet une coloration jaune assez intense, la couleur ambre, d'ailleurs largement utilisée. Elle est en fait liée à la présence de sulfure mais cela ne sera complètement compris qu'au XXe siècle : par extension, une coloration intempestive était attribuée à la présence de carbone.